Coatings for moulding and forming tools
Coatings for molding tools have to meet different requirements compared to coatings for cutting tools - especially important to them besides hardness are smoothness, high elasticity and low coefficient of friction. For this purpose have been developed multilayer coatings based on titanium and chromium compounds with up to 40 layers. It is also possible to apply nanolaminatеs.
For processing of plastics For some of these it is important to provide a low sticking probability (anti-sticking coatings) - for example, the injection of certain types of molding plastics with high coefficient of thermal compression. In this case, the most suitable are carbon-based nanocomposite multilayer coatings with the last layer of non-hydrogenated amorphous carbon. These coatings allow to increase the speed of injection and hence the productivity by 10-15% depending on the operating mode.
Tool: Forming punch
Material: tool steel
Coating: multilayer, Ti/TiN/TiCN/nc-TiCN:a-C/a-C
Hardness: 2500 HV
Coefficient of friction: 0,2
Application: Suitable for injection molding of plastics
Client: Guala Closures Tools Bulgaria
Tool: Forming Punch
Material: tool steel
Coating: Ti/TiN/CrN-ml superlattice
Hardness: 2700 HV
Coefficient of friction: 0,3
Wetting angle: 91°
Application: Suitable for injection moulding of plastics
For processing of metals
Tool: Rolling out mandrel Ф30
Material: HSS
Coating: multilayer, TiN/TiCN/TiN
Hardness: 3000 HV
Application: Suitable for steel forming by spinning
Tool: Forming Mandrel
Material: tool steel
Coating: Ti/TiN/CrN-ml superlattice
Hardness: 3000 HV
Coefficient of friction: 0,27
Wetting angle: 85°
Application: Suitable for deep cold drawing of non-ferrous metal parts
Coatings for molding tools have to meet different requirements compared to coatings for cutting tools - especially important to them besides hardness are smoothness, high elasticity and low coefficient of friction. For this purpose have been developed multilayer coatings based on titanium and chromium compounds with up to 40 layers. It is also possible to apply nanolaminatеs.
For processing of plastics For some of these it is important to provide a low sticking probability (anti-sticking coatings) - for example, the injection of certain types of molding plastics with high coefficient of thermal compression. In this case, the most suitable are carbon-based nanocomposite multilayer coatings with the last layer of non-hydrogenated amorphous carbon. These coatings allow to increase the speed of injection and hence the productivity by 10-15% depending on the operating mode.
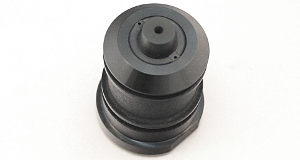
Material: tool steel
Coating: multilayer, Ti/TiN/TiCN/nc-TiCN:a-C/a-C
Hardness: 2500 HV
Coefficient of friction: 0,2
Application: Suitable for injection molding of plastics
Client: Guala Closures Tools Bulgaria
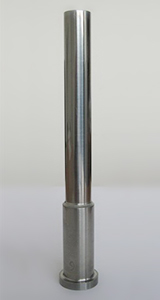
Material: tool steel
Coating: Ti/TiN/CrN-ml superlattice
Hardness: 2700 HV
Coefficient of friction: 0,3
Wetting angle: 91°
Application: Suitable for injection moulding of plastics
For processing of metals
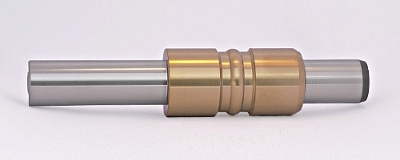
Material: HSS
Coating: multilayer, TiN/TiCN/TiN
Hardness: 3000 HV
Application: Suitable for steel forming by spinning
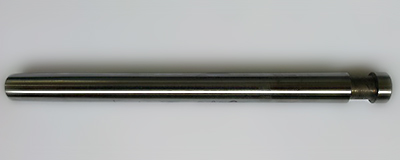
Material: tool steel
Coating: Ti/TiN/CrN-ml superlattice
Hardness: 3000 HV
Coefficient of friction: 0,27
Wetting angle: 85°
Application: Suitable for deep cold drawing of non-ferrous metal parts